World’s tallest wooden wind turbine starts turning
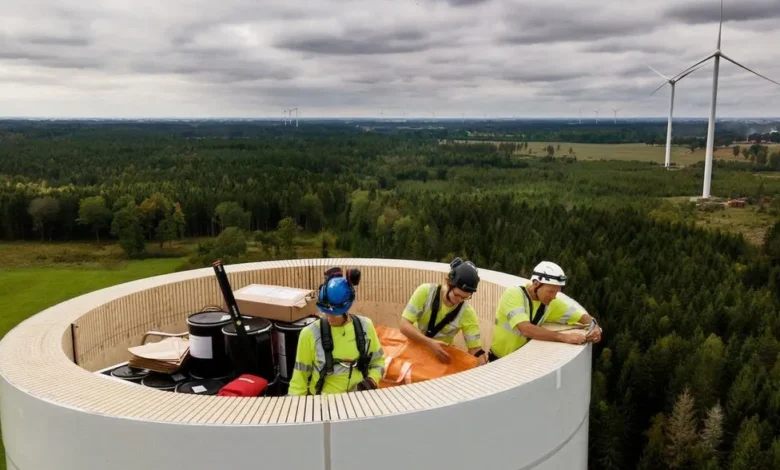
What is made from the same wood as a Christmas tree, held together by glue and manufactured in a Swedish factory for assembly later?
If that calls to mind flat-pack furniture and meatballs, you’re wrong.
If you answered “a wooden wind turbine”, you could be a visionary.
According to Modvion, the Swedish start-up that has just built the world’s tallest wooden turbine tower, using wood for wind power is the future.
“It’s got great potential,” Otto Lundman, the company’s chief executive, says as we gaze upwards at the firm’s brand new turbine, a short drive outside Gothenburg.
It’s 150m (492ft) to the tip of the highest blade and we are the first journalists to be invited to have a look inside. The 2 megawatt generator on top has just started supplying electricity to the Swedish grid, providing power for about 400 homes.
The dream of Lundman and Modvion is to take the wood and wind much higher.
Steel limitations
On the horizon near the Modvion project, several very similar-looking turbines are turning.
Steel, not wood, is the key material for them, as it is for almost all of the world’s turbine towers. Strong and durable, steel has enabled huge turbines and wind farms to be constructed on land and at sea.
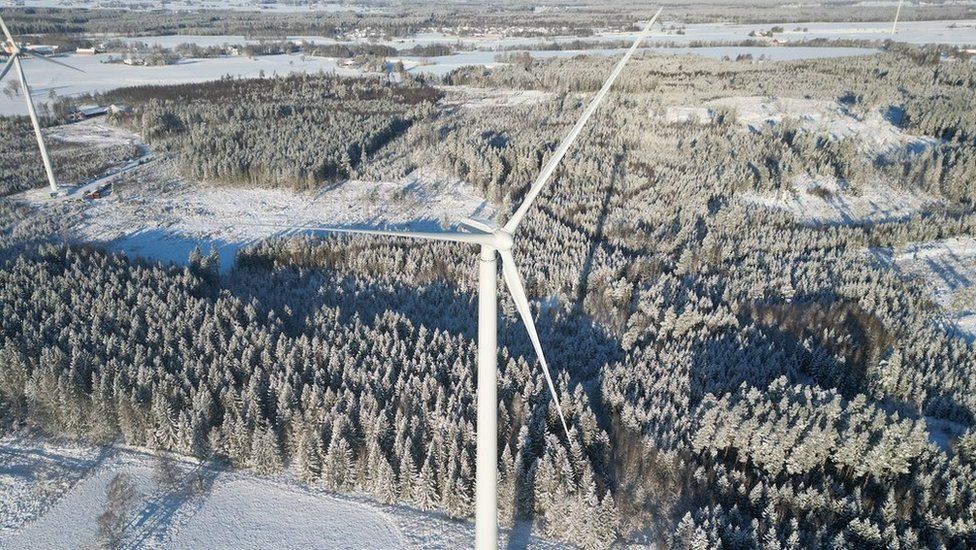
But steel is not without its limitations, particularly for projects on land.
As demand has grown for taller turbines that harvest stronger winds with larger generators, the diameter of the cylindrical steel towers to support them has had to grow too.
In a world of road tunnels, bridges and roundabouts, many in the wind industry say getting those huge pieces of metal to turbine sites has become a real headache, in effect limiting how tall new steel turbines can be.
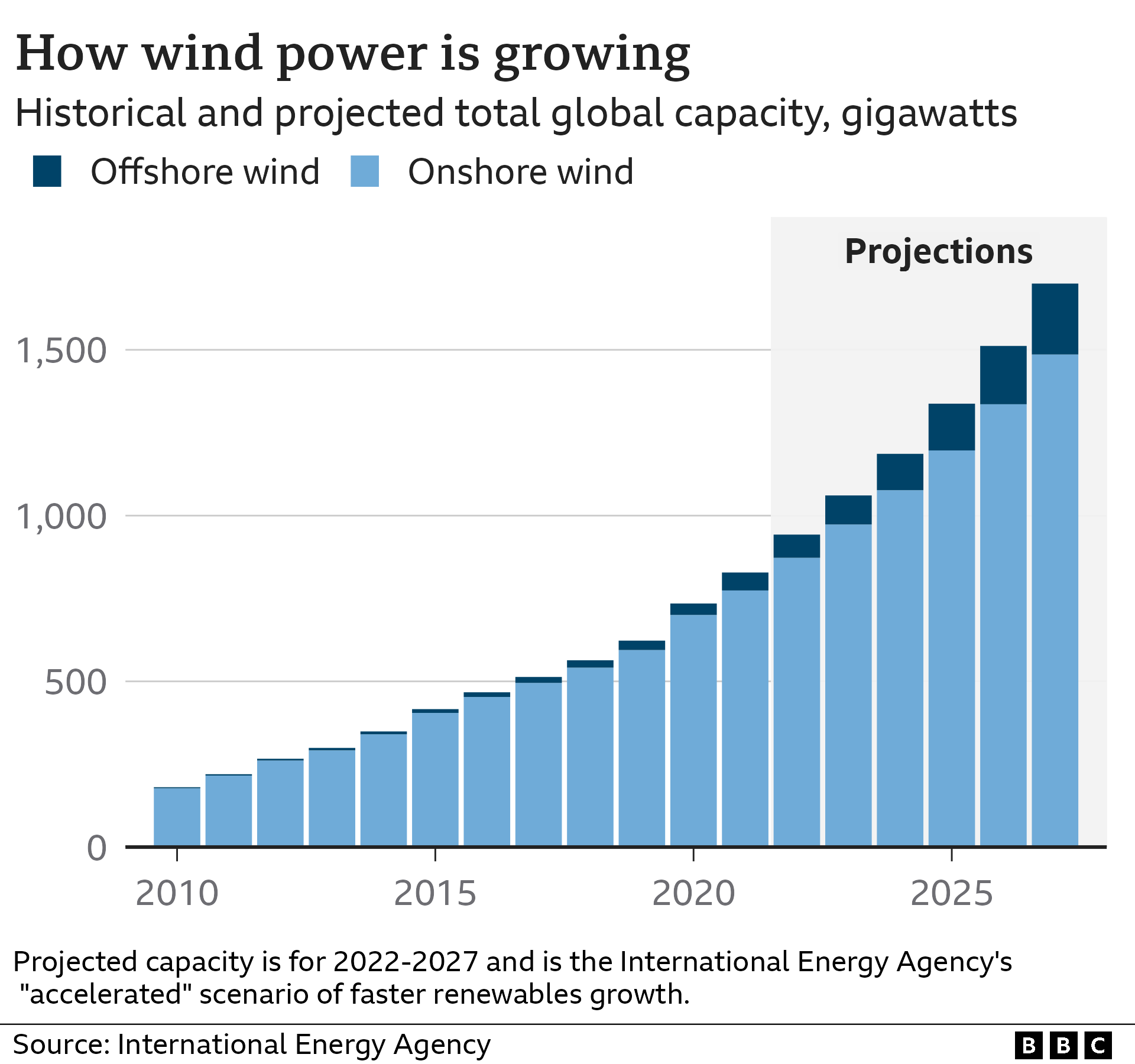
Wooden turbine or sauna?
From the outside, there is little obvious difference between the Modvion wooden turbine and its steel cousins.
Both have a thick white coating to protect them from the elements and blades made primarily from fibreglass attached to a generator, which produces electricity when it turns.
It is only when we go inside the tower that the differences becomes clear. The walls have a curved raw wood finish, not unlike a sauna.
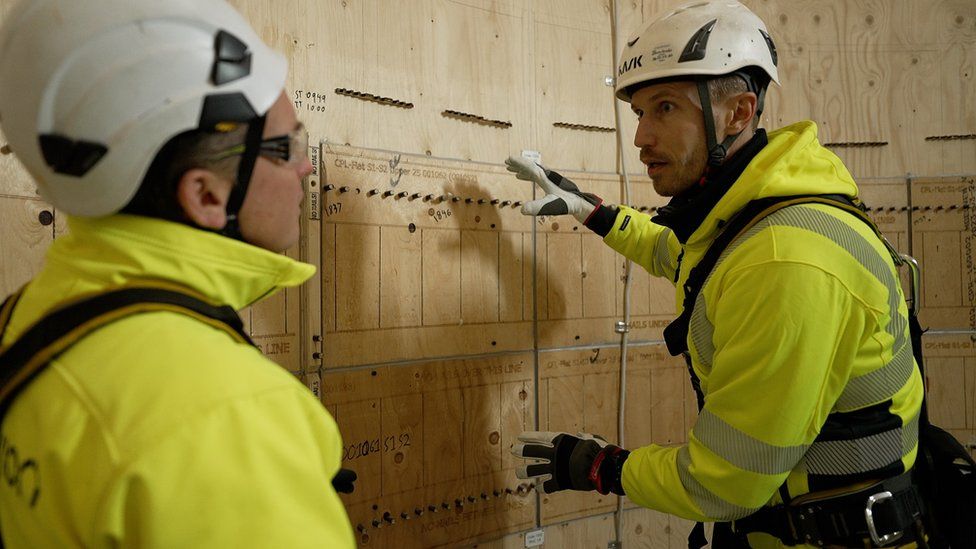
The 105m (345ft) tower’s strength comes from the 144 layers of laminated veneer lumber (LVL) that make its thick walls.
By varying the grain of each of the 3mm-thick layers of spruce, Modvion says it has been able to control the wall’s strength and flexibility. “It’s our secret recipe,” says company co-founder – and former architect and boat builder – David Olivegren, with a smile.
At the factory, on the edge of Gothenburg, the thin layers of wood have been glued and compressed together to make the curved sections. Those pieces are then taken on site, glued together into cylinders and then stacked on top of each other to make the tower.
“Wood and glue is the perfect combination, we’ve known that for hundreds of years,” Olivegren says. “And because using wood is lighter [than steel] you can build taller turbines with less material.”
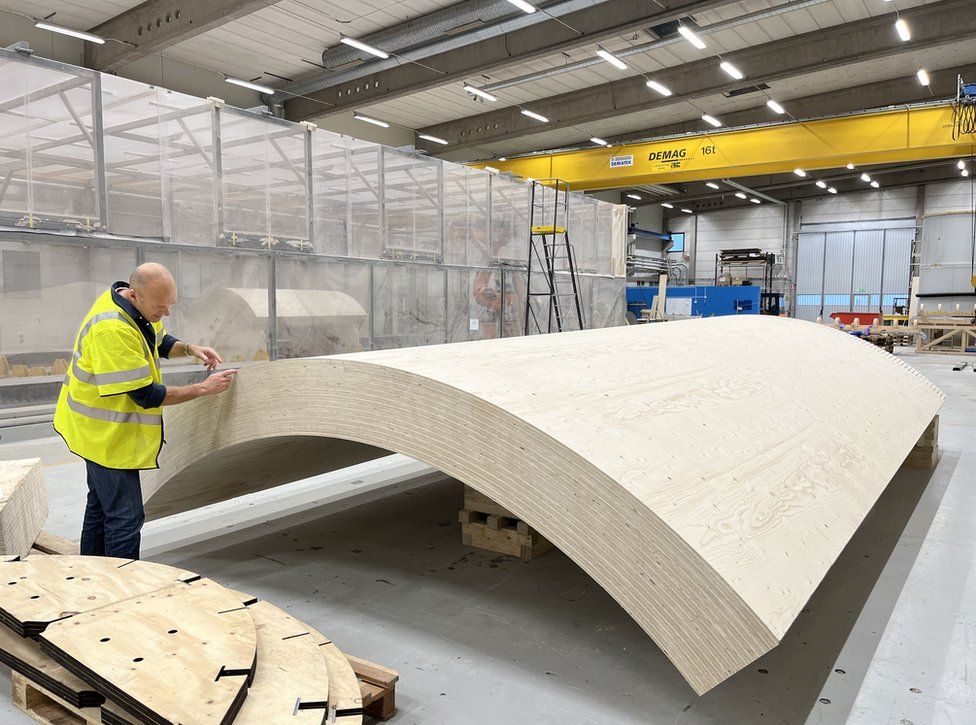
Lundman and Olivegren tell me their turbine’s big selling point is that, by using wood and glue, towers can be built in smaller, more easily transported modules.
That will make it much easier to build really tall towers, they say, and to take the pieces to challenging locations.
However, Dr Maximilian Schnippering, head of sustainability at Siemens Gamesa – one of the worlds largest turbine manufacturers – says more pieces are likely to mean more trucks, more people and more time to complete the installation. He considers the modular system “an advantage” and that wooden towers can “nicely complement” steel towers.
Siemens Gamesa’s efforts are focused on reducing the carbon footprint of the steel it uses, he says.
Inside the Modvion tower, I am shown how the wooden modules have been stacked on top of each other and how they are held by steel fittings that are then glued into place.
“The industry wants to build turbines with a 300m [blade] tip height, which means a tower which is 200m or more in height. With modularity you can do that,” says Lundman.
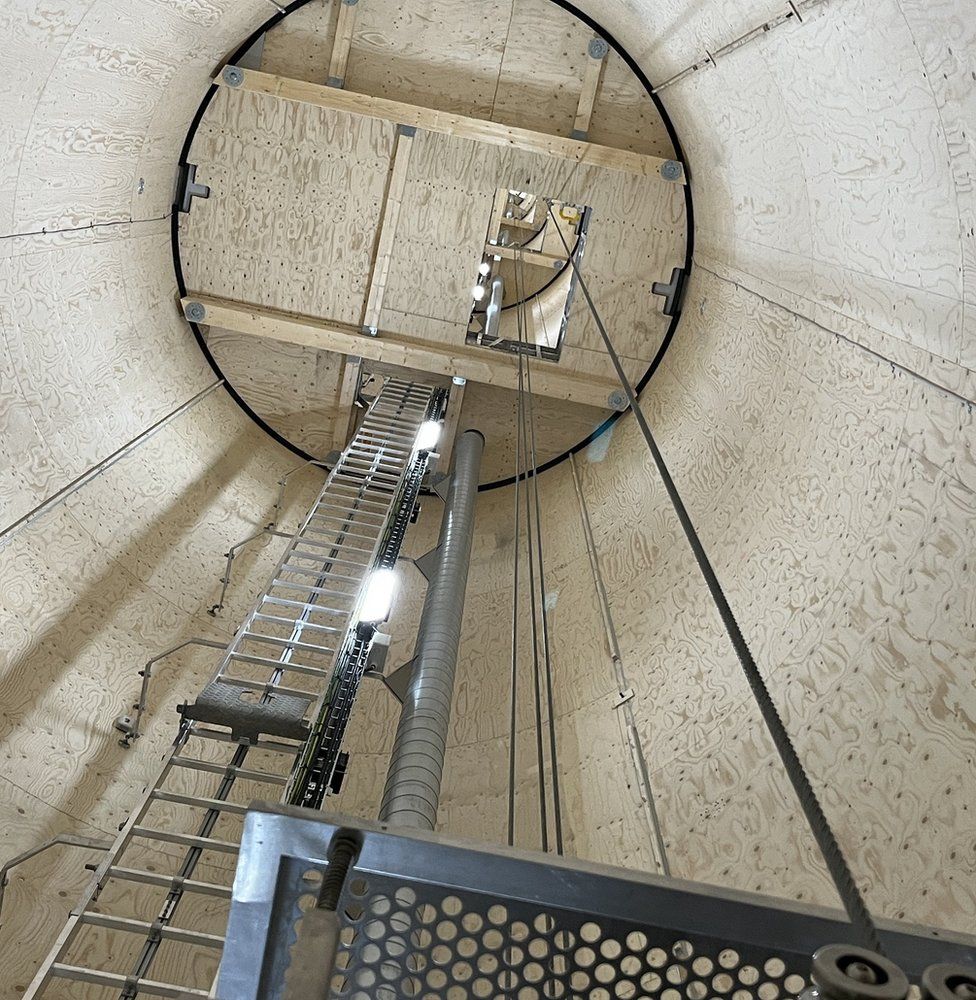
Steel could of course be modular too, with the cylinders cut up into smaller pieces, but the extra effort needed to then bolt the pieces together adds both to costs and to maintenance.
One of the investors in Modvion is renewable energy giant Vestas. It has installed more wind power capacity around the world than any other.
Jan Hagen, its chief technology officer for northern and central Europe, tells me they see “tremendous potential” in the market for taller turbines, with wooden turbines “particularly well suited” to play a role.
“What we find interesting about this is that its combination of an economically viable solution that addresses the transport bottleneck and a sustainable solution,” Hagen says.
Negative carbon footprint
Though wind power is cheaper and cleaner than almost all other forms of electricity generation, making steel involves extremely hot furnaces and almost always the burning of fossil fuels. That means CO2 emissions – the main driver of climate change.
Modvion says using wood instead of steel eliminates the wind turbines’ carbon footprint entirely, making them carbon negative.
That’s because the trees take carbon dioxide out of the atmosphere when they are alive and, when they are chopped down, the carbon is stored in the wood. As long as the wood doesn’t end up rotting or being burned, the carbon is not released.
About 200 trees went into Modvion’s turbine tower. They were the same species – spruce – that is used for Christmas trees and the company says they are farmed sustainably, meaning when they are harvested more are planted.
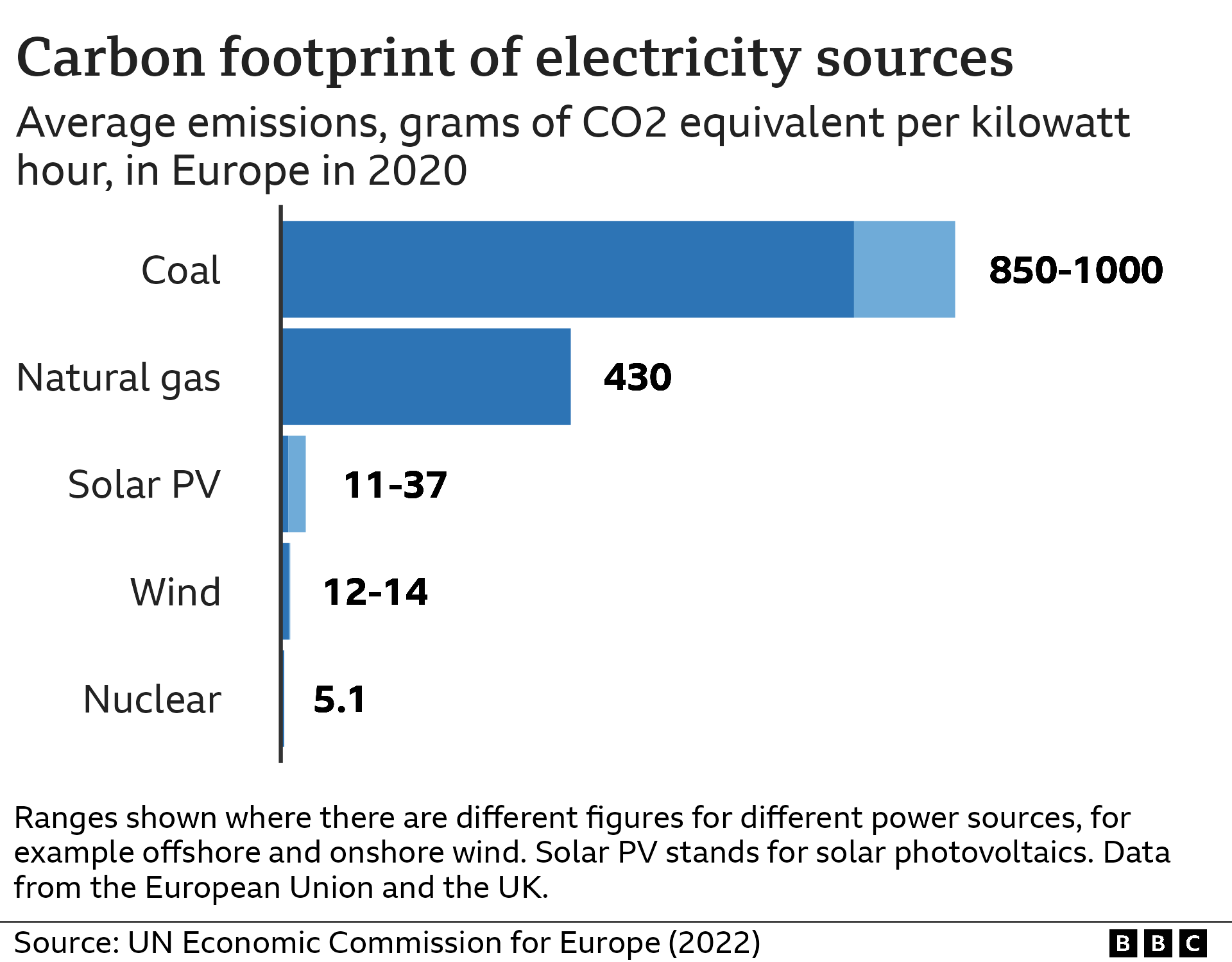
SSE Renewables, one of the UK’s largest producers of wind power, told the BBC it was aware of Modvion’s work and that it would be looking into wooden towers as “an alternative technology” to steel. However, many of SSE’s projects are offshore, which can be reached using huge ships – meaning the modular transport benefits are less pronounced.
Modvion says it is hoping to build another even taller turbine soon and, if all goes well, it will open a facility that will produce 100 wooden modular turbines a year in 2027.
“The industry is currently putting up 20,000 turbines a year,” Lundman says. “Our ambition is that in 10 years time 10% of those turbines – about 2000 – will be wooden.”