Why is the world investing so much in semiconductors?
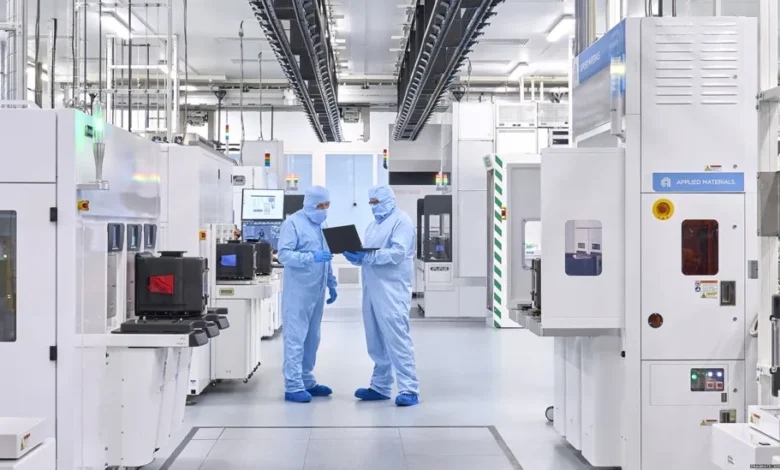
I’m at the UK’s newest computer chip plant in Durham. Formerly a ceramic pipe factory, from the outside it looks like a big warehouse.
But inside the vast space is being transformed into a sophisticated hub for the manufacturing of computer chips.
Pragmatic Semiconductor has already built one production line, which the industry likes to call fabrication lines, or fab lines.
Sealed off in its own large room, the production line has all the expensive machinery needed to make the computer chips, and the air inside is carefully controlled to avoid any contamination during production.
Pragmatic has the money to build another such production line, and funding of £182m ($230m) announced late last year will fund production lines three and four.
As well as from private investors, Pragmatic secured funding from the government-backed UK Infrastructure Bank and British Patient Capital, a subsidiary of British Business Bank.
But the Cambridge-based company will need much more money to complete its plan to build eight production lines in the old pipe factory.
From phones and computers, to cars and washing machines, almost every product with an on-off switch relies on the production of computer chips, also known as semiconductors.
It is an industry that has seen a lot of turbulence over the last few years. There’s been disruption to supply chains during the pandemic, and geopolitical tensions in Asia, where 90% of the world’s most advanced chips originate.
David Moore, chief executive of Pragmatic Semiconductor, which is the largest semiconductor manufacturer in the UK, says the industry is going to need multiple types of semiconductors to solve “different kinds of problems” in the chip sector.
Most semiconductors are made using silicon, but his company is taking a different approach.
They are making flexible chips – they actually bend – at their plant in Durham, which can be used in wearable technology, clothing authentication, and even in parcel labels to track and trace items.
Rather than sitting on silicon wafer, Pragmatic’s chips are built on a flexible thin film.
This approach results in chips that are cheaper and faster to manufacture than the standard silicon chip.
“If you take a standard silicon manufacturing facility, it’s going to take multiple years and billions of dollars to make,” Mr Moore said.
“Our fabrication plant can be 10 to 100 times cheaper depending on what you compare it with.
“In silicon, it will take three to six months to go from the start of the process all the way to a finished wafer product. For us, we can do that in less than 48 hours.”
But it is no panacea. The flexible chip may be cheaper and quicker to make, but the advanced chips in phones, computers and other leading tech will still need the most advanced silicon-based computer chips.