Should more British homes be built using straw?
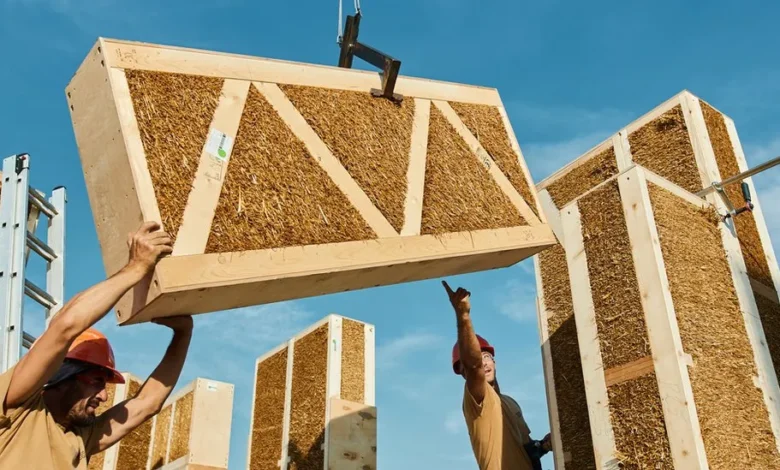
This year, straw from Lithuania will envelop a building in the quiet town of Todmorden, West Yorkshire.
Barbara Jones and her colleagues at Todmorden Learning Centre and Community Hub have hatched a plan to clad the college, built in the 1950s, in more than 1,600 sq metres of straw-stuffed panels – to better insulate it.
“We’re going to make it a showcase,” says Ms Jones, an expert on natural building materials.
The panels will be supplied by EcoCocon, a Slovakian firm that has appointed Ms Jones as one of its technical sales consultants. Each timber-framed panel is around 400mm thick and contains a mass of chopped straw – essentially, a slightly more high-tech version of the simple straw bales that have been used by some eco-friendly builders for decades.
Such solutions have been around for years and other firms are selling similar products, but, with rising demand for insulation and sustainability, EcoCocon is now targeting larger-scale projects. The question is whether straw, a millennia-old building material, can scale up to meet 21st Century ambitions.
In panel systems, relatively short pieces of straw are packed together at just the right density, about 110 kg per metre cubed, so that the volume of air inside creates an insulating effect. Ms Jones says this also protects against fire. Loose straw, in contrast, is notoriously flammable.
Another handy feature is that the panels can be prepared with the straw protruding slightly. This means they can be pushed against an uneven wall and still form a tight seal – think of the pin art toys you press your hand or face into to make an impression of them.
“It will take up the unevenness without you having to put a plaster layer on first – which is a massive cost saving,” says Ms Jones. She adds that the cost of the panels is not significantly more than many non-natural insulation options, and estimates that it would be possible to build a single house featuring straw insulation panels for about £2,000 per square metre.
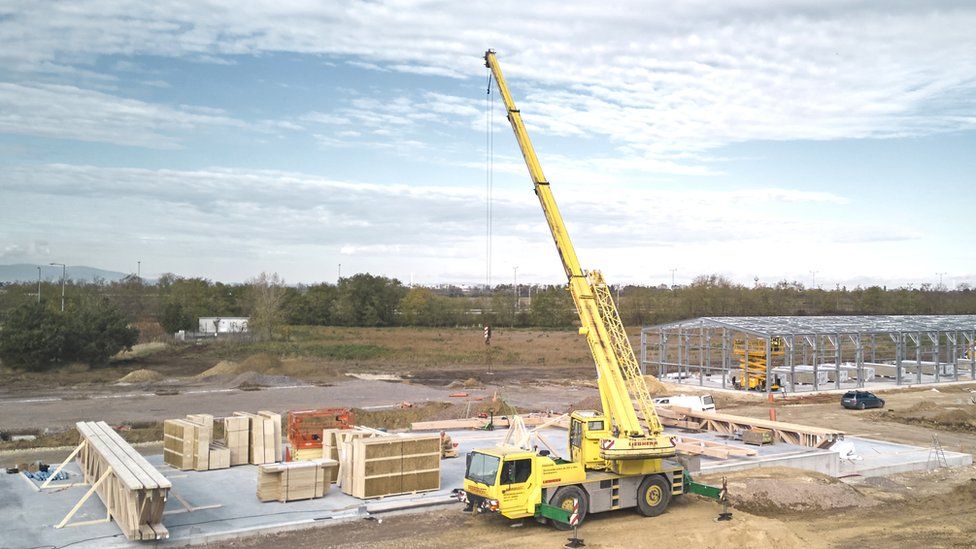
Key to EcoCocon’s expansion strategy is the launch of a new highly automated factory in Slovakia, due to open by the end of the year. Chief executive Bjørn Kierulf said that it will include robots and a fully digitised process. Straw will be locally sourced in Central and Eastern Europe, stuffed into panels, and then shipped to customers in the UK, for example.
There are limitations. Ms Jones says that using the panels for retrofitting smaller properties is unlikely to be a good idea, given their significant width of 400mm. It could make old walls unreasonably thick.
When it comes to new builds, however, rival firm Agile Property and Homes, which offers straw-stuffed panels previously marketed under the brand name ModCell, argues that incoming construction standards are likely to demand higher insulation levels in walls. Therefore, thicker walls might become more common no matter what material you choose. Straw-insulated homes might not, then, seem uniquely chunky in the near future.
The UK produces roughly nine million tonnes of straw annually as an agricultural byproduct, says Agile’s business development director Finlay White: “Nine million tonnes is enough to build detached houses – an average three-bedroom detached house – 436,000 of them insulated with straw.”
Agile is currently planning to insulate 115 properties this year, a mix of residential, commercial and educational buildings. “We’re looking to more than double, if not treble, capacity,” says Mr White.
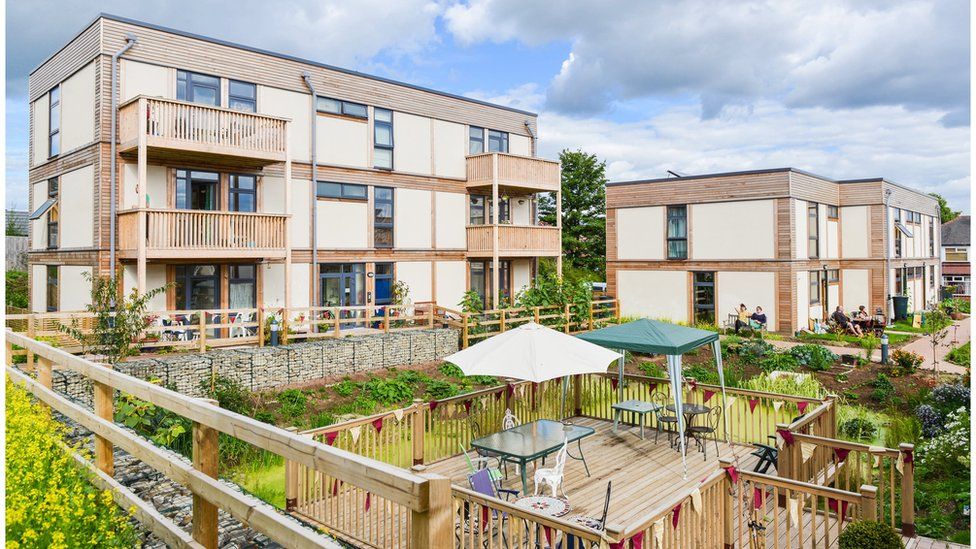
Consumers may be hesitant about buying a home built with lots of straw in the walls, suggests Richard Fitton, an expert in building physics at the University of Salford. There could be concerns about rodents nesting in the material or problems with the straw becoming damp and mouldy – all issues dismissed by Ms Jones and other proponents, who argue that these are not common or insurmountable problems.
However, insurers might take a different view and jack up premiums for people whose homes are built using less common materials or methods of construction. “Insurers will want to be confident about how resilient these building materials are and how they might react in a fire, storm, flood, or to extreme temperatures, damp and subsidence,” says Louise Clark, general insurance policy adviser at the Association of British Insurers.
Prof Fitton says that, from a personal point of view, building with natural materials is desirable, though he adds, “Do I see the mass house-builders taking it on tomorrow? No, I probably don’t.”